Ⅲ Main Equipments
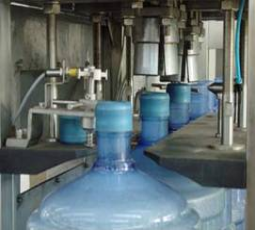
1. De-capper
General Description
TBG300 de-capper is the de-capping device developed according to requirement of high-speed 5 gallon barreled water line. The de-capping elevation, tension and barrel blocking mechanism use free-lubrication cylinder, no oil pollution, clean and tidy.
Main Features
1) Use free-lubrication cylinder, no oil pollution, clean and tidy.
2) Adopt adjustable barrel blocking arm.
3) Stainless steel structure, beautiful and easy to clean.
4) Outer Brusher
Brief Introduction
WST300 outside brusher is the cleaning equipment developed according to the high speed trend and demand of 5 gallon barreled water line.
Main Features
1) Rotary cleaning and conveying mechanism with simple structure easy for maintenance.
2) Adopt gear transmission, fast and stable.
3) Stainless steel structure, beautiful and easy to clean.
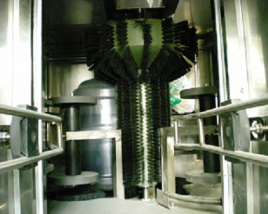
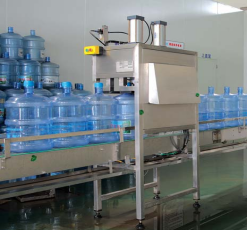
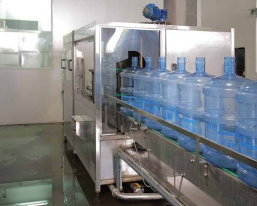
2.QGF-300 Rinser/Filler/Capper
General Description
QGF300 rinser/filler/capper monobloc is advanced equipment developed on base of international advanced technology and according to the trends of high speed and automation development for beverage in China.
Main Compositions
Rinsing/filling/capping monobloc is composed of automatic bottle loader, rinser, pipe system, conveying mechanism, filler, and detection device.
Automatic Bottle Loader
General Description
1) The machine base is composed of stainless steel plate and stainless steel square pipe. It has advantages of high intensity, good rigidity, light weight, beautiful appearance, good observation and easy cleaning.
2) The bottle loading mechanism adopts 90°cylinder overturning mechanism, stable and reliable.
3) Bottle feeding and pushing mechanism is composed of bottle pushing rack and bottle pushing cylinder. Its function is to push bottles on bottle-n conveyor to the bottle loading hopper.
Working Principle
Empty bottles are sent to bottle loading conveyor from bottle-in conveyor. After bottles touches the travel switch on bottle loading conveyor, PLC do counting operation. When calculating 4 bottles are ready, the bottle feeding and pushing mechanism cylinder acts to push bottle pushing rod to push the empty bottles on bottle loading conveyor to bottle loading hopper. The bottle is upright in the hopper and the bottle loading detection sensor detects that the bottle in the hopper has been ready and sends signal immediately to make the up bottle overturning cylinder act to push bottle loading hopper turns 90°and turns the bottle to level position. At this moment, the bottle mouth faces to the positive direction of bottle fixing cup of the rinser’s conveyor. The bottle pushing & loading sensor detects the bottle has been ready and bottle pushing & holding cylinder acts to push the bottle into the fixing cup of rinser’s conveyor and realizes level loading bottles. The rinser’s conveyor is driven by rinser driving mechanism and empty bottles go forward to the machine body.
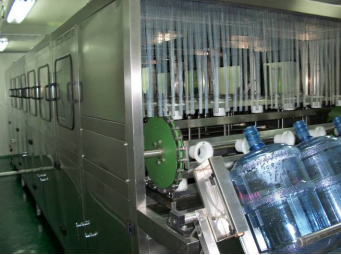
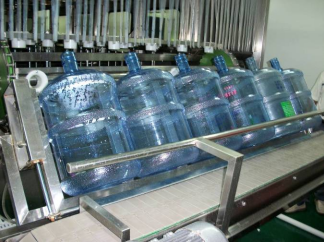
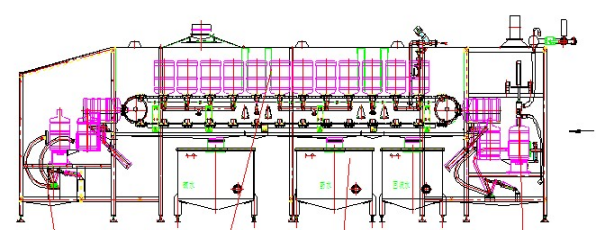
Rinser
General Description
1) The rinser base is welded with bended stainless steel plate and stainless steel square pipe. It has advantages of beautiful appearance, high intensity, good rigidity, light weight and easy cleaning.
2) The rinser conveyor is composed of active and passive sprocket, chain, bottle holding plate and bottle fixing cup. The chain and sprocket are well designed to make them more scientific and perfect.
3) The rinser driving mechanism is pushed by cylinder to make the bottle in each working position stay for certain time. The chain is calculated strictly according automatic bottle loading and dropping positions to ensure exact position of the whole automatic running.
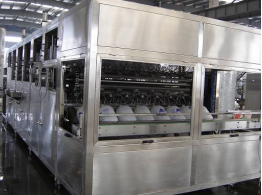
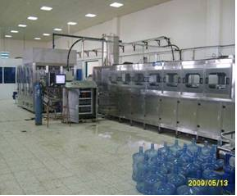
Filler/Capper
General Description
1) Filler base is welded with bended stainless steel plate and stainless steel square pipe. It has advantages of beautiful appearance, high intensity, good rigidity, light weight and easy cleaning.
2) The filling valve adopts the newest filling head. While filling, the cylinder makes down movement, and filling sports valves body touches the bottle mouth to compress the spring and open filling valve.
3) Cap container is used for storing and sending caps. When cap sorter needs caps supplement, the cap elevator conveys caps to the cap container which slides caps stably and quickly into the cap sorter.
4) Cap sorter is mainly composed of motor rotating tray, cap chute and shell. Its function is to bring caps in the box into cap chute by motor round tray rotating and make caps in the chute downward and rank in order by special mechanism.
5) Capper base is welded with stainless steel plate and stainless steel square pipe. It has advantages of beautiful appearance, high intensity, good rigidity, light weight and easy cleaning.
6) Capping mechanism is to do capping for the filled bottle with cap to achieve sealing effect. It adopts pre-cap type capping.
7) Bottle down mechanism is composed of bottle holding hopper, bottle down rack and bottle down cylinder. It adopts 90°cylinder overturning structure, stable and reliable.
8) Bottle-out pushing mechanism is composed of bottle pushing plate, bottle pushing rack and bottle pushing cylinder. It is mainly for pushing the clean bottle onto conveyor.
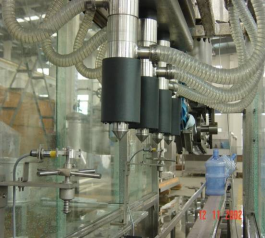
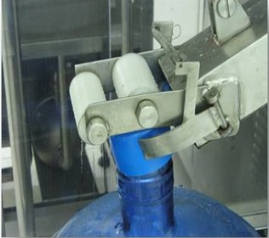
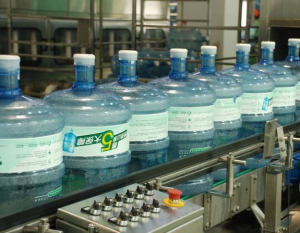
3. Barrel Conveyor
General Description
The speed capacity efficiency is related to the conveyor collocation .It’s a must to consider the temporary stop which should not affect the previous section running and also the coordination with the left part. Our production line layout fully considers the client investment and using efficiency.
It brings in the Germany technique and developed the design. Most of the parts adopt the punching and bending, which has good rigidity, lighter and easier exchange. Stable transportation ,easy maintenance ,applicable for diameterφ40~φ110 mm bottle. It’s equipped with full bottle sensor in each section, All the section are linkage control. , which meets the demand for the trace.
Main Features
1) Model: SC00
2) Material: stainless steel
3) Empty barrel conveyor motor: 0.55KW/unit
4) Full barrel conveyor motor: 1.1KW/unit
4. Light Inspection
Brief Introduction
Light inspection box is covered with stainless steel, with appropriate and comfortable light of national sanitary standard, which can inspect clearly the impurity, defaults and grains.
Technical Data
● Power of light pipe: 20W
● Number of light pipe: 3
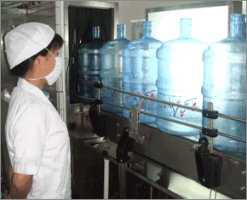
5.Automatic gallon film package machine
1. Packaging efficiency is high, mechanized operation reduces labor costs; packaging speed can reach 600 barrels/hour to 2500 barrels/hour, saving two to four workers, saving labor costs of about 100,000 yuan per year, but also greatly reducing the cost of bags. The cost of the membrane of the old five gallon bucket lifter is 0.1 corner, and the cost of the membrane of the fully automatic bagging machine is 6-8 points.
2. After shrinkage sealing, the bucket bag fits the outer edge of the bucket, which is beautiful and compact.
3. Plastic film can protect the bucket and reduce wear.
The main features of the barreled water automatic bagging machine are as follows:
1. Conveying system: Frequency conversion can speed up operation.
2. Main frame: 304 stainless steel frame.
3. Hot-cutting cooling mode: medium pressure air-dry cooling.
4. Sleeve mode: Stepping motor assisted film entry mode.
5. Sealing mode: electric wire pressure hot-cutting bag sealing mode.
6. Barrel feeding mode: automatic detection of barrel feeding, automatic transmission.
7. Equipment specifications: 3500 mm * 850mm * 1600 mm, 600 mm conveyor belt off the ground.
8. Applicable product specifications: 5 gallon barrel or custom barrel. Uniform specifications are required.
9. Membrane specifications: 680-720 mm in length, 0.006-0.015 mm in thickness, 350 mm in diameter, no static electricity, tightly wound.
10. Maximum load of transportation operation: 20KG/0.5m/s.
11. Safety protection: mechanical protection.
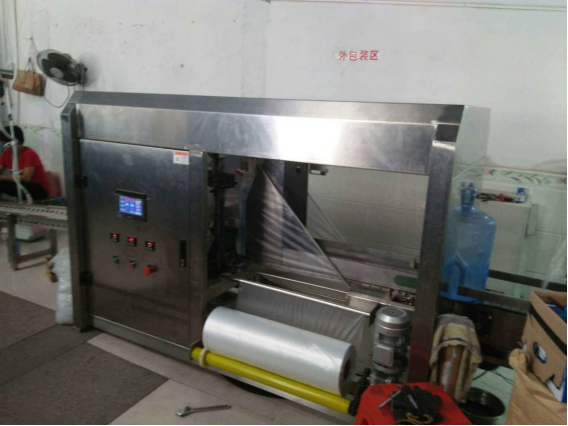
Post time: Nov-30-2022